Ensuring workplace safety begins with understanding how to identify fire hazards in the workplace. Identifying and addressing these risks is critical to protecting employees, property, and overall business operations. Ignoring fire hazards can lead to devastating consequences, including severe injuries, loss of life, extensive property damage, financial losses, and even legal liabilities for non-compliance with safety regulations. Recognizing potential risks early on is essential for maintaining a safe working environment.
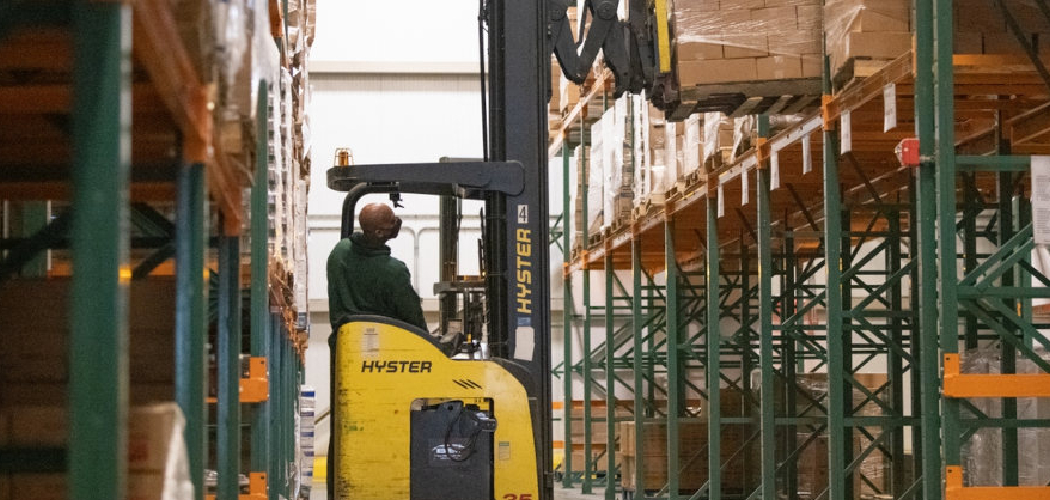
This article provides a comprehensive guide to help businesses and employees understand and mitigate fire risks. It covers common fire hazards found in various workplaces, practical inspection methods to spot these dangers, and proactive strategies for prevention. By following these guidelines, organizations can foster a safer, more secure workplace for everyone involved.
Understanding Fire Hazards
Definition of Fire Hazards
A fire hazard refers to any situation, material, or condition that increases the likelihood of a fire starting or spreading. These hazards typically involve three essential components—sources of ignition, fuel, and oxygen—which together create the potential for combustion. Ignition sources can include hot surfaces, open flames, or electrical sparks. Fuel refers to any combustible material, such as paper, wood, or flammable liquids, while oxygen is naturally present in the air, sustaining the fire.
The Fire Triangle
The fire triangle is a fundamental concept in fire safety that illustrates the three essential elements required for a fire to ignite and continue burning—heat, fuel, and oxygen. Removing or controlling any one of these components disrupts the triangle and prevents the fire from starting or spreading. Understanding the fire triangle is crucial in identifying hazards and implementing effective preventive measures.
Common Categories of Fire Hazards
Fire hazards are commonly classified into three primary categories:
- Electrical Hazards – Includes exposed wiring, overloaded circuits, and malfunctioning equipment.
- Chemical Hazards – Refers to flammable liquids, gases, and reactive substances that can ignite under improper storage or handling.
- Physical Hazards – Encompasses materials like paper or textiles, as well as heat-producing equipment capable of sparking fires.
By recognizing these categories, individuals and organizations can take targeted actions to mitigate fire risks in the workplace.
How to Identify Fire Hazards in The Workplace: Common Fire Hazards in the Workplace
Understanding common fire hazards in the workplace is pivotal for ensuring safety and preventing devastating incidents. These hazards generally fall into distinct categories, each requiring specific prevention strategies to minimize risk.
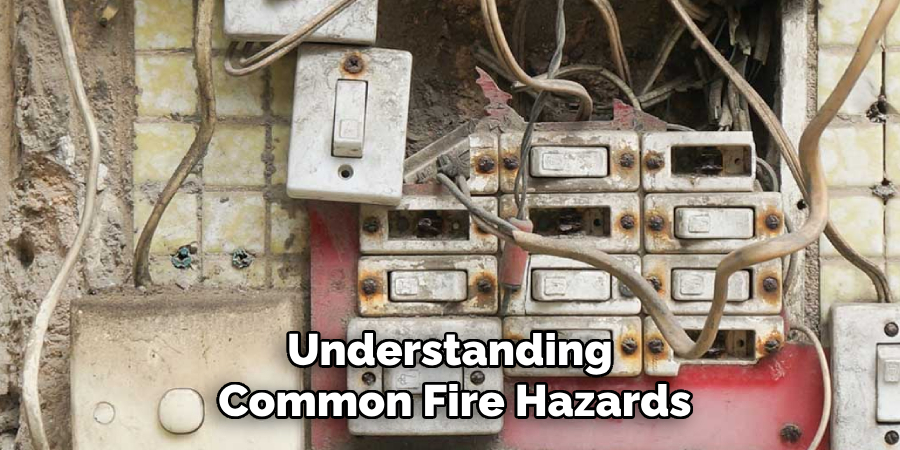
Electrical Hazards
Electrical hazards are a leading cause of workplace fires. Key risks include overloaded circuits, which can overheat and cause sparks, and faulty wiring, which may degrade over time or become damaged due to improper installation. Additionally, the improper use of electrical equipment—such as using devices with damaged cords, neglecting regular inspections, or exceeding the voltage capacity of electrical outlets—can significantly increase the chances of an electrical fire. To mitigate these risks, workplaces should conduct frequent electrical maintenance, ensure compliance with safety regulations, and provide adequate training on proper equipment usage.
Chemical Hazards
Chemicals pose significant fire risks, especially when flammable liquids, gases, or reactive substances are involved. Improper storage—such as placing incompatible chemicals near one another, using substandard containers, or exposing chemicals to heat sources—can trigger ignition. Flammable gases, if leaked, can create highly combustible environments. Employees must be trained in proper chemical handling procedures, and workplaces should utilize clearly labeled, fire-resistant storage units. Installing proper ventilation systems can further reduce the risk of accidents caused by chemical hazards.
Physical Hazards
Physical hazards in the workplace often contribute to fire risks when the environment is not properly maintained. Cluttered workspaces, for example, can obstruct pathways and fuel a fire’s spread. Blocked exits present major safety concerns as they hinder evacuation during emergencies. Likewise, improper storage of combustible materials, like paper, textiles, or packaging, near heat sources or electrical equipment significantly elevates fire risks. Practicing regular housekeeping, maintaining clear escape routes, and ensuring proper storage practices can help address these issues.
Human Factors
Human error and negligence are frequent contributors to workplace fires. A lack of training or awareness regarding fire safety protocols can lead to improper handling of hazardous materials or equipment. Failing to turn off electrical appliances, ignoring warning signs of potential hazards, or misusing flammable substances all increase the likelihood of a fire incident. Organizations must invest in ongoing fire safety training programs, enforce strict adherence to safety measures, and foster a workplace culture that prioritizes vigilance and accountability.
By addressing these fire hazards—from electrical and chemical risks to physical and human factors—workplaces can create safer environments for employees and reduce fire incidents. Proactive measures and education are the most effective tools for mitigating these risks.
How to Conduct a Fire Hazard Assessment
Conducting a comprehensive fire hazard assessment is critical in identifying potential risks and implementing appropriate safety measures. A well-structured approach ensures that no hazards are overlooked and supports effective mitigation strategies.
Preparation for Inspection
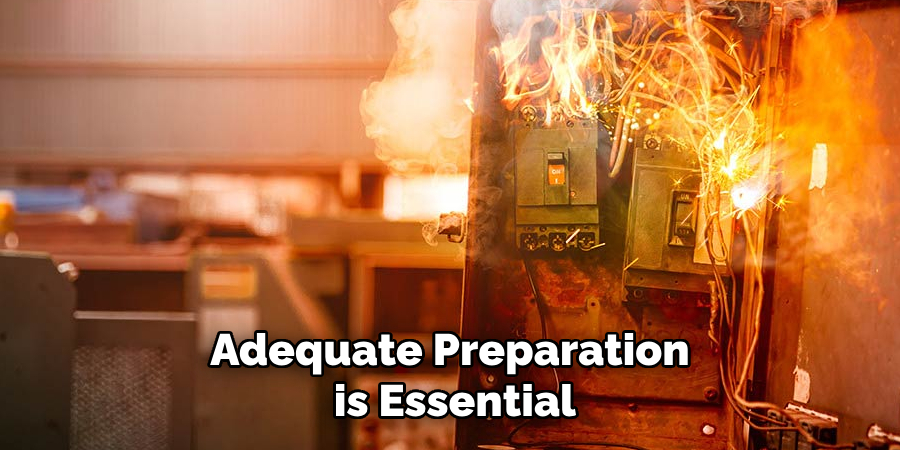
Before beginning the assessment, adequate preparation is essential to ensure an efficient process. Start by creating a checklist of potential hazards tailored to the specific workplace type. For example, an office environment might focus on electrical equipment and blocked exits, while a manufacturing site may emphasize flammable materials and machinery. Gather necessary tools, such as flashlights, for inspecting poorly lit areas, and ensure you have access to essential documents like fire safety plans and floor layouts. Thorough preparation helps streamline the inspection process and ensures all critical areas are addressed.
Systematic Inspection Process
The inspection should follow a systematic and methodical approach to evaluate every workplace area thoroughly. Begin by walking through the workplace systematically, covering one section at a time. Pay special attention to high-risk zones such as kitchens, storage areas with combustible materials, and mechanical rooms where machinery or electrical systems may pose a threat. Look for signs of potential hazards, including exposed wiring, overloaded circuits, improperly stored chemicals, or blocked emergency exits. A consistent inspection process reduces the chance of missing significant risks.
Documenting Findings
Recording identified hazards and their specific locations is a crucial step in the assessment process. Detailed documentation ensures that all risks are accounted for and tracked for corrective action. Write clear and concise descriptions of each hazard, supported by photographs where applicable, to provide additional context. Keeping accurate records not only aids in planning mitigation strategies but also reinforces accountability and facilitates future review.
Risk Prioritization
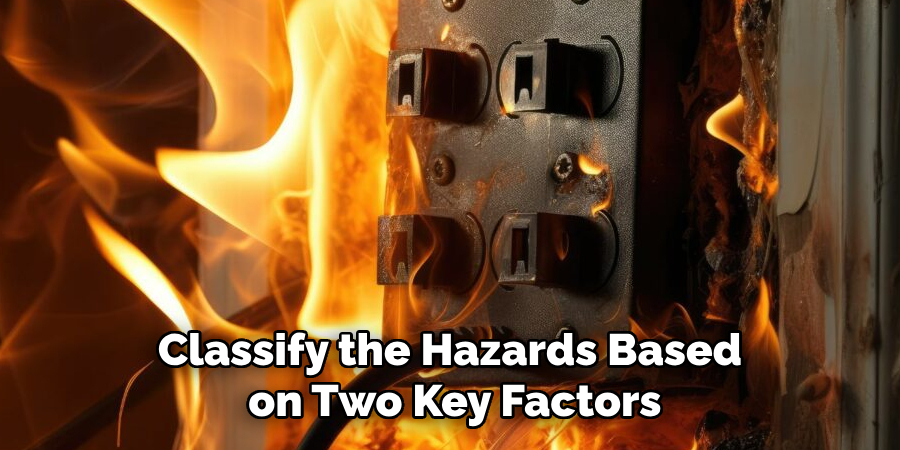
Once the inspection is complete, classify the hazards based on two key factors: their likelihood of occurrence and potential severity. This prioritization helps direct resources toward addressing the most critical risks first. For instance, an overloaded electrical circuit in a high-traffic area would typically demand immediate attention compared to a minor obstruction in a low-traffic storage room. Creating an actionable mitigation plan based on priority ensures that the most pressing issues are resolved promptly, reducing the chance of fire incidents.
By following these steps—preparation, systematic inspection, detailed documentation, and risk prioritization—organizations can conduct thorough fire hazard assessments and build safer workplaces for everyone.
Preventive Measures to Minimize Fire Hazards
Implementing preventive measures is crucial to minimize fire hazards in any workplace. Below are key practices to enhance safety and reduce risk factors:
Electrical Safety Protocols
Regular maintenance of electrical equipment is essential to prevent malfunctions that could spark fires. Ensure all devices are inspected periodically, wires are intact, and faulty equipment is repaired or replaced promptly. Avoid overloading circuits, which can lead to overheating and potential electrical fires. Additional measures to ensure electrical safety include using surge protectors and adhering to the recommended voltage limits.
Proper Storage Practices
Flammable materials must be handled carefully and stored in designated, ventilated areas away from heat sources. Use clearly labeled storage cabinets specifically designed for chemicals or combustibles, and ensure compliance with local fire codes. Additionally, storage areas should be kept organized to reduce the potential for fire spread.
Workplace Organization
Maintaining a clean and organized workspace is a simple yet vital fire prevention measure. Clutter not only obstructs walkways and workspaces but can also fuel fires. Regularly declutter and ensure emergency exits and escape routes are always accessible and unblocked.
Employee Training
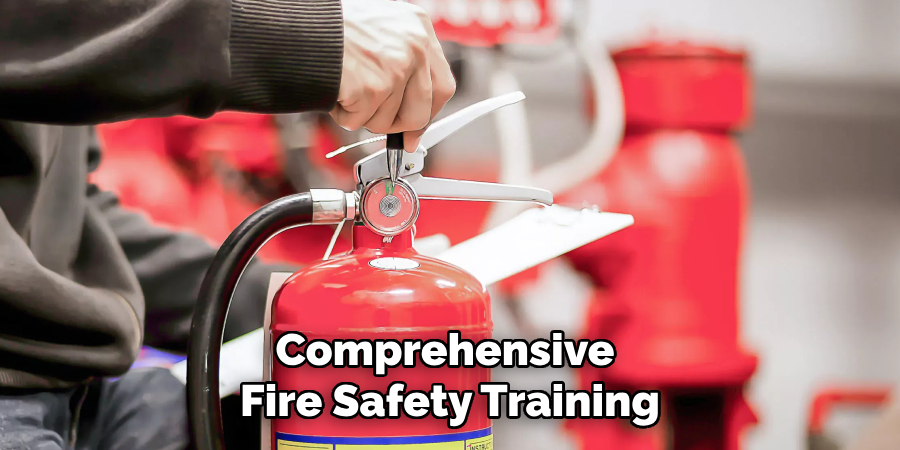
Comprehensive fire safety training is essential for all employees. Regular drills help familiarize staff with evacuation procedures, while training on using fire extinguishers and handling equipment safely empowers them to respond efficiently in emergencies. A well-trained workforce is central to maintaining a safe and hazard-free workplace.
Fire Safety Equipment and Systems
Smoke Detectors and Alarms
Maintaining functional smoke detection systems is critical for early fire detection and warning. Smoke detectors and alarms provide the first alert in a fire, allowing occupants to evacuate promptly and mitigating potentially catastrophic damage. Regular maintenance, including testing and battery replacement, ensures these systems remain operational and reliable.
Fire Extinguishers
Fire extinguishers are vital tools for controlling small fires before they escalate. It is essential to place different types of extinguishers in accessible locations tailored to address potential fire hazards specific to the workplace environment, such as those involving electrical equipment or flammable liquids. Clear labeling and staff training on proper extinguisher use further enhance workplace safety.
Sprinkler Systems
Automatic sprinkler systems are key in suppressing fires effectively and minimizing damage. These systems activate quickly when heat is detected, releasing water to control and extinguish flames before they can spread. Regular inspections and maintenance of sprinkler systems ensure they remain in optimal working condition, adding a layer of protection to fire safety measures.
Emergency Lighting and Signage
Functional emergency lighting and clearly visible exit signage are critical for preventing confusion and ensuring safe evacuation during emergencies. These systems guide occupants to exits even in low visibility conditions caused by power failures or smoke. Periodically testing and maintaining these systems safeguard their functionality when needed most.
Regular Monitoring and Reassessment
Periodic Inspections
Scheduling regular inspections is essential for identifying new hazards that may arise over time. Changes in the workplace, such as installing new equipment, introducing different materials, or evolving processes, can create unforeseen risks. Routine evaluations ensure fire safety measures remain effective and relevant, adapting to these changes before they become critical issues.
Updating Safety Plans
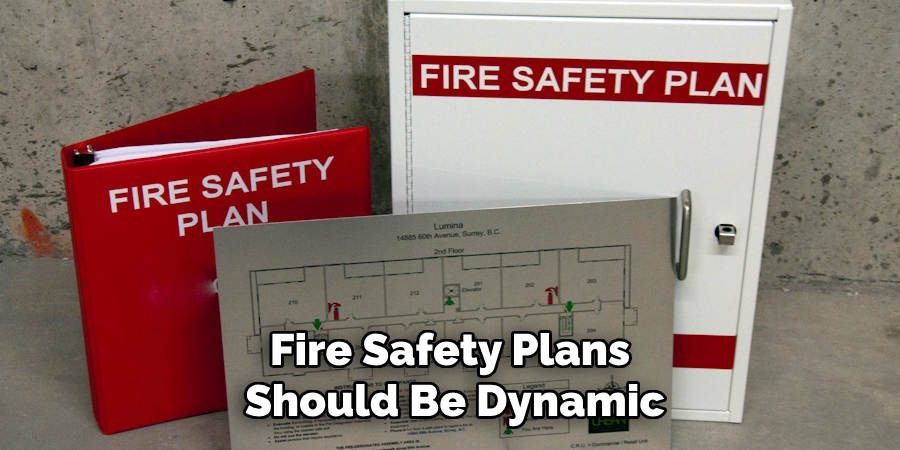
Fire safety plans should be dynamic documents that evolve alongside workplace adjustments. Revisiting and revising these plans becomes imperative whenever there are changes to the physical layout, operational procedures, or occupancy levels. This proactive approach maintains an up-to-date emergency response system tailored to the current conditions of the environment.
Employee Feedback
Encouraging employees to report potential hazards or unsafe practices fosters a culture of safety and vigilance. Workers are often the first to notice subtle issues, and their insights can play a pivotal role in preventing serious incidents and maintaining a safe workspace.
Conclusion
Proactively identifying and mitigating fire hazards in the workplace is essential to safeguarding lives, property, and business continuity. Regular inspections and effective preventive measures are key to maintaining a safe environment. Employees play a crucial role by staying vigilant and reporting potential risks, fostering a safety culture. Understanding how to identify fire hazards in the workplace empowers both management and staff to take immediate, corrective action. By prioritizing these efforts, organizations can significantly reduce the likelihood of accidents and ensure a secure workplace for everyone. Take action today to address risks and create a safer environment.