Safety is a critical component in the construction industry, where workers often face hazardous conditions. Conducting a hazard assessment is an essential step to identify, evaluate, and mitigate risks on construction sites. This proactive approach not only ensures compliance with safety regulations but also protects workers from potential injuries and fosters a culture of safety.
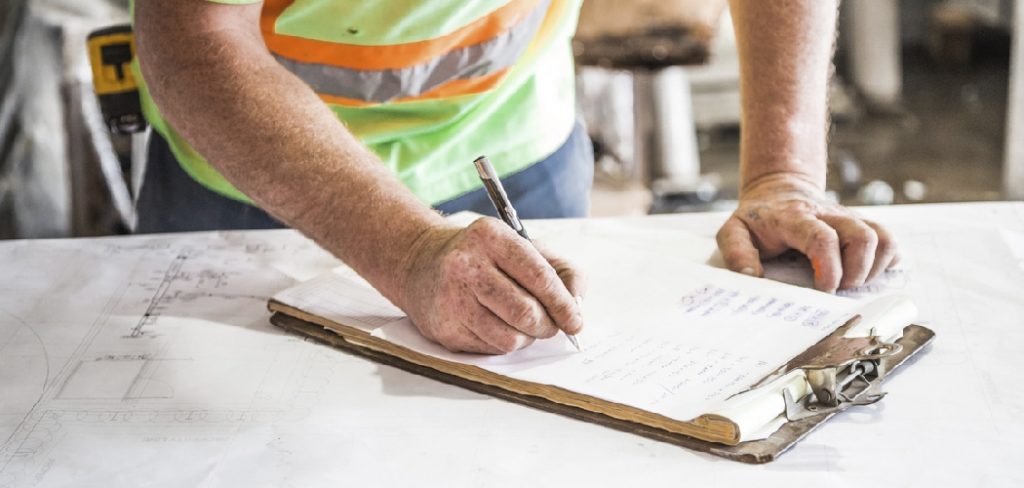
This guide is designed to help you with how to conduct a hazard assessment in construction. By systematically analyzing the environment, equipment, and processes, hazard assessments help create safer and more efficient operations for everyone involved.
The Importance of Hazard Assessment in Construction Projects
Hazard assessments play a crucial role in ensuring the safety and success of construction projects. They help identify potential risks early, allowing project managers to implement measures to prevent accidents and injuries. By addressing hazards proactively, these assessments reduce downtime caused by workplace incidents, leading to more efficient project timelines and cost savings. Furthermore, conducting regular hazard assessments demonstrates a company’s commitment to worker safety and compliance with occupational regulations, improving morale and fostering trust among employees. Ultimately, prioritizing hazard assessments ensures a safer work environment and contributes to the overall quality and reputation of the project.
Steps for Conducting a Hazard Assessment in Construction
Conducting a hazard assessment in construction requires a structured and systematic approach to ensure all potential risks are identified and addressed. Below are the key steps to performing an effective hazard assessment:
- Review Job Tasks and Worksite Conditions
Begin by analyzing the specific tasks that will be performed on the construction site. Identify the tools, equipment, and materials involved, as well as the physical conditions of the worksite, such as terrain, weather, and existing infrastructure. This initial review helps pinpoint potential hazards tied to specific activities.
- Identify Potential Hazards
Look for risks related to physical, chemical, biological, or ergonomic factors that could harm workers. Common construction hazards include falls, exposure to harmful substances, electrical risks, and machinery malfunctions. Consulting historical data from past projects can also help identify patterns of risk.
- Assess the Level of Risk
Once hazards are identified, evaluate the probability and severity of potential incidents. Use risk assessment tools such as a risk matrix to prioritize hazards based on their likelihood and potential impact, focusing on high-risk areas that require immediate attention.
- Develop Control Measures
Create strategies to mitigate or eliminate identified risks. This may involve implementing engineering controls, modifying work procedures, providing personal protective equipment (PPE), or enhancing worker training. Collaboration with safety experts can help ensure appropriate measures are robust and effective.
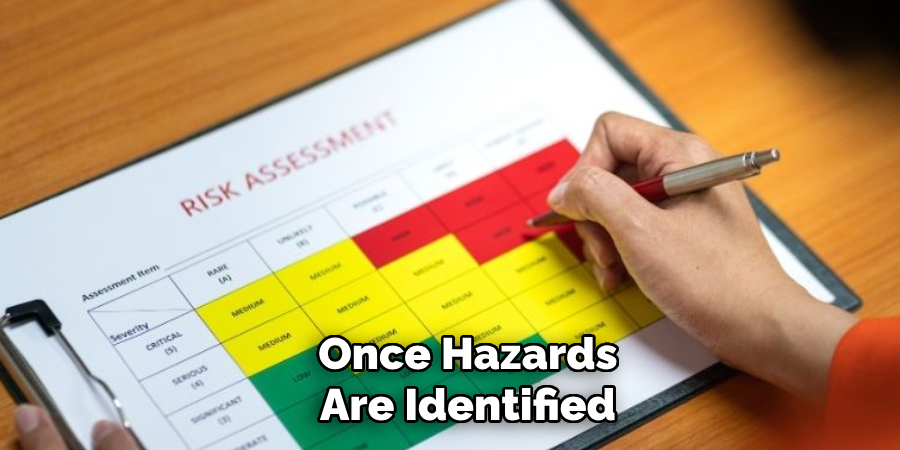
- Communicate and Train
Share the hazard assessment findings with all workers and stakeholders involved in the project. Clearly outline the risks and the measures put in place to manage them. Provide proper training to ensure everyone understands how to follow safety protocols and use equipment or PPE correctly.
- Monitor and Reassess Regularly
Hazard assessments are not a one-time task. Conditions on construction sites can change rapidly, introducing new risks. Regularly review and update the hazard assessment to ensure it remains relevant and effective, especially when new tasks, equipment, or materials are introduced.
10 Methods How to Conduct a Hazard Assessment in Construction
1. Understand the Scope of the Project
Begin the hazard assessment by thoroughly understanding the construction project’s scope, timeline, and tasks involved. Review project plans, blueprints, and schedules to identify high-risk activities such as excavation, heavy equipment operation, or working at heights. Recognizing the scope allows you to anticipate potential hazards associated with each phase of the project. This foundational step ensures a targeted and efficient assessment.
2. Perform a Site Walkthrough
Conduct a detailed walkthrough of the construction site to observe existing conditions and identify visible hazards. Examine the terrain, evaluate access points, and assess the layout for potential risks such as uneven ground, debris, or inadequate lighting. Pay attention to areas with heavy machinery or materials handling, as these are common sources of accidents. Document findings and take photos or videos to provide a visual record for later analysis.
3. Engage Workers and Supervisors
Workers and supervisors are often the first to notice potential hazards due to their daily tasks. Engage them in discussions about workplace safety to identify risks that may not be immediately visible during a walkthrough. Use surveys, interviews, or informal conversations to gather insights on unsafe practices, faulty equipment, or environmental conditions. Involving workers fosters a culture of safety and ensures a more comprehensive hazard assessment.
4. Identify Job-Specific Hazards
Break down each job or task into individual components to identify specific hazards associated with them. For example, scaffolding assembly involves risks like falling objects, structural instability, and improper use of tools. Use a Job Hazard Analysis (JHA) to systematically evaluate each task, highlighting potential dangers and determining preventive measures. This focused approach ensures no detail is overlooked during the assessment.

5. Assess Chemical and Material Risks
Construction projects often involve the use of hazardous materials such as adhesives, solvents, or asbestos-containing products. Review the Material Safety Data Sheets (MSDS) for all chemicals used on-site to understand their properties and associated risks. Identify safe handling, storage, and disposal practices to prevent accidents like spills, fires, or toxic exposure. Proper chemical management is essential for safeguarding workers and the environment.
6. Evaluate Machinery and Equipment
Inspect all machinery and equipment on-site to ensure they are in good working condition. Look for signs of wear and tear, faulty components, or improper maintenance. Check that safety guards, emergency stop buttons, and warning labels are intact and functioning. Ensure operators are properly trained and certified to use the equipment. Regular inspections and maintenance minimize the risk of accidents caused by mechanical failures.
7. Examine Environmental Factors
Environmental conditions play a significant role in construction site safety. Assess the site for hazards such as extreme temperatures, strong winds, or proximity to water bodies. Consider how weather changes might affect worker safety, such as slippery surfaces during rain or reduced visibility in fog. Implement appropriate measures, like providing weather-appropriate gear or scheduling work to avoid hazardous conditions, to mitigate environmental risks.
8. Analyze Ergonomic Risks
Physical strain and repetitive motions can lead to musculoskeletal injuries, a common issue in construction. Assess tasks that require heavy lifting, awkward postures, or prolonged standing to identify ergonomic risks. Provide workers with proper lifting techniques, tools like hoists or carts, and adjustable workstations where possible. Addressing ergonomic risks improves worker comfort and reduces the likelihood of injury.
9. Review Emergency Preparedness
Evaluate the construction site’s readiness to handle emergencies such as fires, medical incidents, or equipment malfunctions. Ensure that first aid kits, fire extinguishers, and emergency exits are easily accessible and in good condition. Verify that workers are trained in emergency procedures, including evacuation drills and first aid protocols. A well-prepared site can respond effectively to emergencies, minimizing harm and damage.
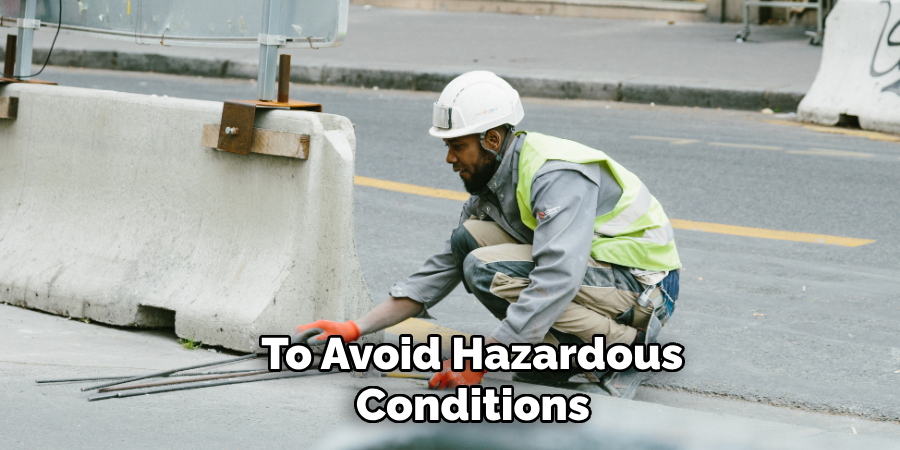
10. Develop a Risk Mitigation Plan
After identifying hazards, develop a comprehensive risk mitigation plan tailored to the construction project. Prioritize hazards based on their severity and likelihood of occurrence, then implement control measures such as engineering solutions, administrative policies, or personal protective equipment (PPE). Regularly review and update the plan as the project progresses or new risks emerge. A proactive approach ensures continuous safety improvements on-site.
Things to Consider When Conducting Hazard Assessments
When conducting hazard assessments in construction, there are several key factors to keep in mind to ensure effectiveness and thoroughness:
- Frequency of Assessments: Hazard assessments should not be a one-time activity. Regular evaluations are necessary, especially as the project evolves, new phases begin, or worksite conditions change. Periodic reviews help address emerging risks promptly.
- Worker Training and Awareness: Ensure that all workers are trained to recognize hazards and understand safety protocols. Their active participation and awareness significantly enhance the accuracy and practical value of the hazard assessment process.
- Documentation and Record-Keeping: Maintain comprehensive records of hazard assessments, including identified risks and implemented control measures. This documentation ensures accountability and provides a valuable reference for future projects or audits.
- Compliance with Regulations: Always align the hazard assessment process with local, state, and federal safety regulations. Compliance not only avoids legal issues but also ensures industry-standard safety practices are being followed.
- Use of Technology: Leverage modern technology such as drones, sensors, and software tools to improve efficiency and accuracy in identifying and managing hazards. These tools provide real-time data and analysis that enhance decision-making.
- Emergency Protocols: Incorporate emergency scenarios into hazard assessments to evaluate the site’s preparedness for unforeseen events. This ensures that safety measures cover both routine tasks and potential emergencies.
By considering these factors, construction managers can conduct more effective hazard assessments, leading to safer workplaces and reduced risks for everyone involved.
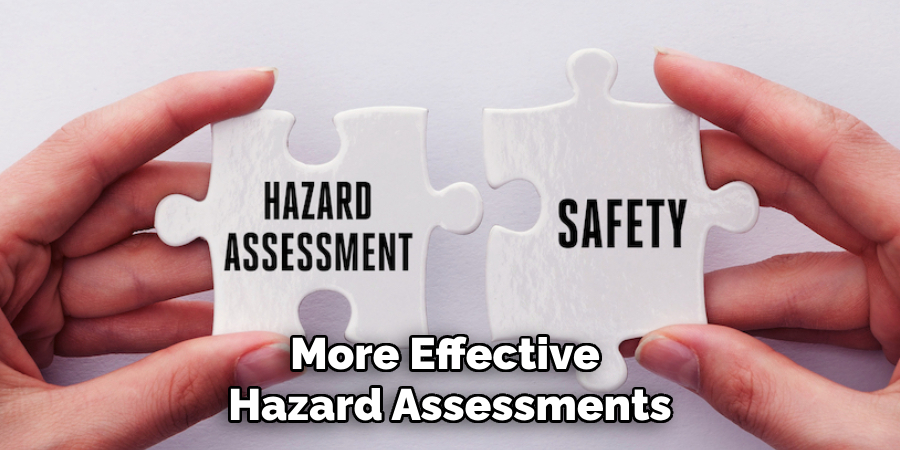
Conclusion
Conducting a hazard assessment in construction is a multi-faceted process that requires careful observation, collaboration, and planning. By understanding the project scope, involving workers, evaluating machinery, and addressing environmental and chemical risks, you can create a safer work environment. Each of the ten methods outlined here contributes to a thorough hazard assessment that not only prevents accidents but also fosters a culture of safety and responsibility in construction projects. Thanks for reading our blog post on how to conduct a hazard assessment in construction! We hope you found it helpful and informative.