Laboratories are essential spaces for scientific discovery and innovation, but they often involve working with hazardous chemicals that pose serious risks if not handled properly. Effective management of chemical hazards is crucial to ensure the safety of personnel, protect the environment, and maintain compliance with regulatory standards. By understanding the potential dangers and implementing best practices, lab users can minimize risks and foster a safe and productive workspace. This guide provides an overview of how to manage chemical hazards in the lab.
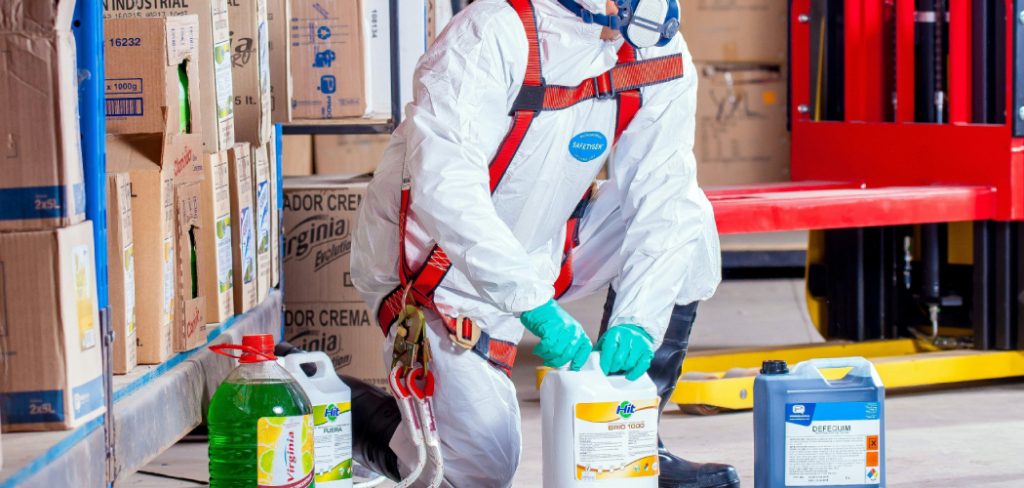
Types of Chemical Hazards
Chemical hazards in the laboratory can be categorized into several types based on the nature of the risks they pose. Understanding these categories is essential for properly assessing and mitigating potential dangers:
- Toxic Substances
These chemicals can cause harm to health when inhaled, ingested, or absorbed through the skin. Examples include solvents, heavy metals, and certain gases, which can lead to acute or chronic health effects depending on the level of exposure.
- Flammable and Combustible Materials
These substances can ignite easily and pose fire or explosion hazards. Common examples include alcohols, acetone, and other volatile organic compounds. Proper storage and handling are critical to reduce the risk of accidental ignition.
- Corrosive Chemicals
Corrosive substances, such as acids and bases, can damage skin, eyes, respiratory tissue, and even equipment. Examples include hydrochloric acid, sodium hydroxide, and sulfuric acid. Personal protective equipment (PPE) and proper ventilation are vital when working with these materials.
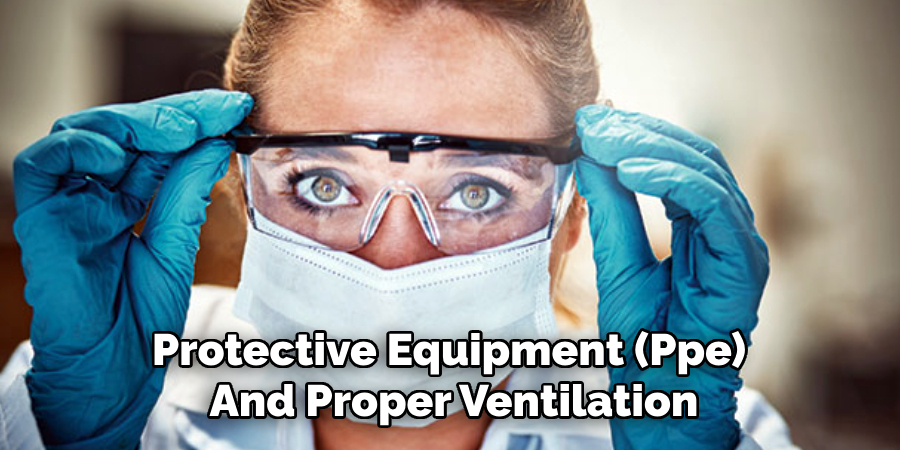
- Reactive Chemicals
These compounds may react violently when exposed to air, water, or other incompatible substances. Reactive chemicals, such as sodium metal or peroxides, require special handling and storage procedures to avoid unplanned reactions.
- Carcinogens, Mutagens, and Reproductive Toxins
Some chemicals, such as benzene, formaldehyde, or certain pesticides, have long-term effects on health by potentially causing cancer, genetic mutations, or harming reproductive systems. It is critical to limit exposure and monitor usage strictly.
By understanding and identifying these types of chemical hazards, laboratory personnel can implement appropriate safety measures to reduce risks and ensure a secure working environment.
10 Methods How to Manage Chemical Hazards in the Lab
1. Conduct Comprehensive Risk Assessments
Before starting any lab work, perform a detailed risk assessment for all chemicals involved. Identify the potential hazards, such as toxicity, flammability, or reactivity, and evaluate the level of risk associated with each. Utilize Material Safety Data Sheets (MSDS) to gather specific information about the chemicals. By assessing risks in advance, you can implement appropriate safety measures tailored to the unique challenges of each substance.
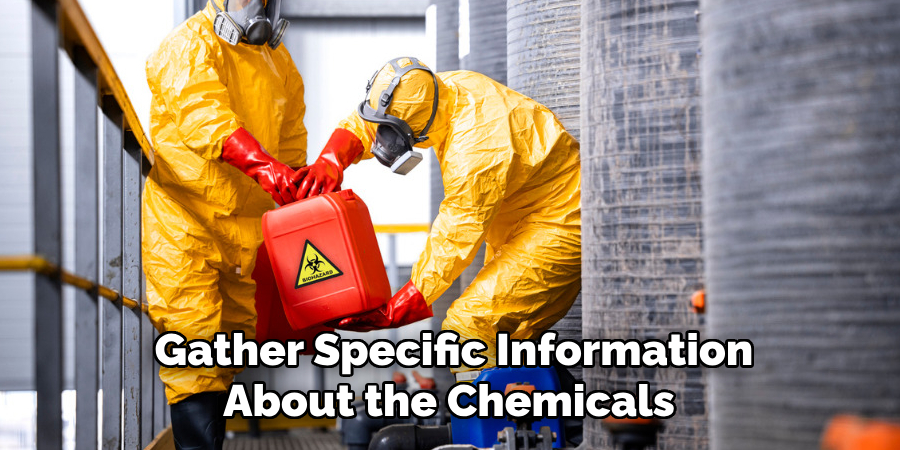
2. Implement Proper Storage Practices
Proper storage is critical for managing chemical hazards. Segregate chemicals based on their compatibility—flammables, oxidizers, acids, and bases should never be stored together. Use ventilated cabinets for volatile substances and ensure all containers are clearly labeled. Avoid overstocking to minimize the risk of spills and make emergency response easier. Adhering to proper storage protocols reduces the likelihood of accidents and ensures quick access to necessary materials.
3. Provide Adequate Ventilation
Many chemicals release hazardous fumes that can harm lab personnel. Ensure the lab is equipped with proper ventilation systems, such as fume hoods and exhaust fans, to remove harmful vapors from the workspace. Conduct regular maintenance checks to confirm these systems are functioning effectively. Adequate ventilation not only protects individuals but also prevents the accumulation of flammable or reactive gases.
4. Use Personal Protective Equipment (PPE)
The proper use of Personal Protective Equipment (PPE) is a cornerstone of chemical hazard management. Equip lab personnel with gloves, safety goggles, lab coats, and, when necessary, respiratory protection. Match the PPE to the specific chemicals being handled, as different substances require different levels of protection. Regularly inspect PPE for wear and replace damaged items promptly. Ensuring proper use of PPE significantly reduces exposure risks.
5. Train Staff on Chemical Safety
Effective management of chemical hazards begins with informed staff. Provide comprehensive training on chemical handling, storage, and emergency response procedures. Emphasize the importance of understanding MSDS information and recognizing hazard symbols. Regularly update training sessions to cover new chemicals or procedures introduced in the lab. A well-trained team is better equipped to prevent accidents and respond appropriately if they occur.
6. Develop and Enforce Standard Operating Procedures (SOPs)
Create clear and detailed Standard Operating Procedures (SOPs) for all activities involving hazardous chemicals. Include step-by-step instructions for handling, transferring, and disposing of chemicals safely. Ensure that all lab personnel are familiar with these SOPs and enforce compliance. SOPs provide a consistent framework for safe practices, reducing the likelihood of errors or unsafe shortcuts.
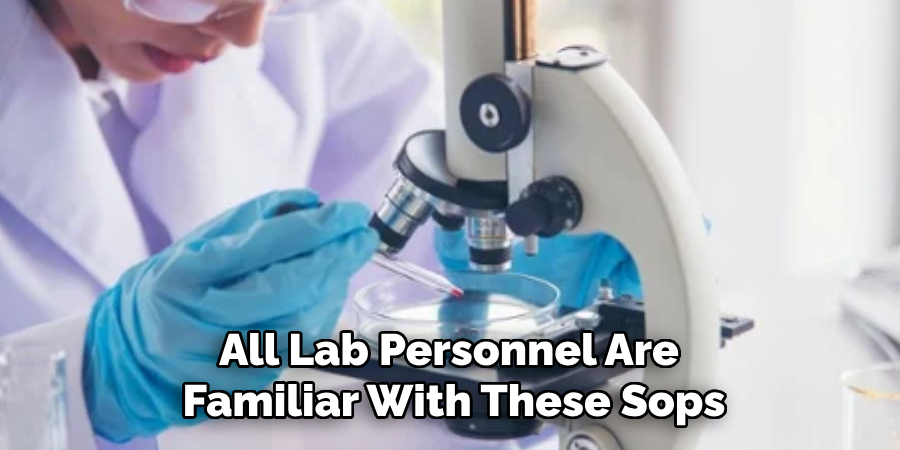
7. Ensure Proper Chemical Labeling
Accurate labeling of chemicals is vital for hazard identification. Use standardized labels that include the chemical name, concentration, hazard symbols, and precautionary statements. For solutions or mixtures prepared in the lab, create custom labels with the same level of detail. Regularly inspect containers to ensure labels remain legible and intact. Proper labeling prevents confusion and enables swift action in case of an emergency.
8. Maintain Readiness for Emergencies
Emergencies involving chemical hazards can escalate quickly, making preparedness essential. Equip the lab with fire extinguishers, eyewash stations, and chemical spill kits, ensuring they are easily accessible. Conduct regular drills to practice emergency response scenarios, such as spill containment or evacuation. Familiarity with emergency procedures enables lab personnel to act decisively and minimize harm during incidents.
9. Adopt Proper Disposal Practices
Improper disposal of chemicals can pose significant environmental and safety risks. Follow local regulations and institutional guidelines for disposing of hazardous waste. Segregate waste into appropriate categories and use designated containers to prevent chemical reactions. Label waste containers clearly and arrange for regular collection by certified disposal services. Proper disposal ensures the safe removal of hazardous materials from the lab environment.
10. Conduct Routine Audits and Inspections
Regular audits and inspections are essential for identifying and addressing potential hazards. Evaluate storage areas, PPE, ventilation systems, and emergency equipment to ensure compliance with safety standards. Involve lab personnel in the inspection process to foster a culture of accountability. Document findings and implement corrective actions promptly. Routine evaluations help maintain a safe and hazard-free lab environment.
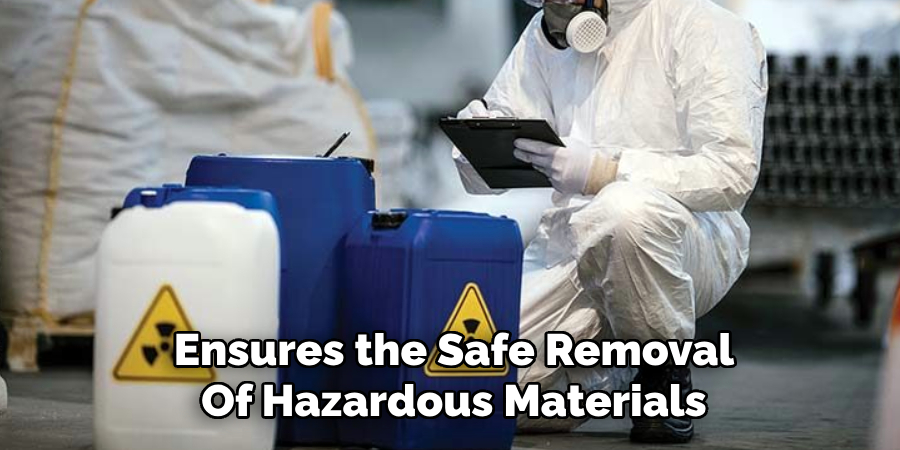
Maintenance and Upkeep
Proper maintenance and upkeep are critical for sustaining a safe and efficient laboratory environment. All equipment, safety devices, and infrastructure must undergo regular assessments to ensure they remain in optimal condition. Develop a structured maintenance schedule that includes inspections of fume hoods, ventilation systems, and emergency equipment, such as eyewash stations and fire extinguishers. Replace or repair damaged or aging safety apparatus promptly to avoid failures during critical moments. Additionally, keep an accurate record of maintenance activities and updates to ensure compliance with safety regulations and standards. By prioritizing maintenance and upkeep, laboratories can minimize risks and maintain a secure workspace for all personnel.
Troubleshooting Common Issues
Despite rigorous safety measures, laboratories may occasionally encounter challenges that require immediate attention and effective troubleshooting. Here are some common issues and strategies to address them:
- Malfunctioning Ventilation Systems
If fume hoods or exhaust fans fail to operate correctly, first check for power supply issues or blockages in the air ducts. Ensure filters are clean and replaced as needed. Inform maintenance personnel promptly if the problem persists, as prolonged malfunctions can increase exposure to hazardous fumes.
- Damaged or Worn-Out PPE
Regularly inspect all personal protective equipment for signs of wear, such as tears in gloves or scratched safety goggles. Replace damaged items immediately and ensure that high-quality PPE is always stocked. Provide staff with proper training to identify wear and handle PPE with care.
- Improper or Insufficient Chemical Labeling
Labels may fade or fall off over time, leading to confusion and safety risks. Inspect all chemical containers regularly and reapply clear, comprehensive labels when necessary. Implement a labeling system that includes routine checks to prevent such occurrences.
- Emergency Equipment Failure
Failing fire extinguishers, eyewash stations, or spill kits can pose serious risks during critical moments. Schedule frequent inspections of all emergency equipment. Address malfunctions by either repairing the faulty components or replacing the equipment altogether without delay.
- Chemical Spill or Release
Spills can happen even in the most meticulously organized setups. Ensure spill kits and containment tools are accessible, and train all personnel on their proper use. Isolate the spill area immediately and ventilate the space as needed. Follow established protocols for cleanup to prevent further exposure or reactions.
- Noncompliance with SOPs
Deviations from Standard Operating Procedures can lead to errors or incidents. Conduct regular refresher training sessions to reinforce the importance of adhering to SOPs. Encourage open communication so that staff can seek clarification or raise concerns about procedural issues.
- Unanticipated Chemical Reactions
Accidental mixing of incompatible chemicals can result in dangerous reactions. Immediately evacuate the area if such an incident occurs and follow spill or containment protocols. Conduct post-incident investigations to understand the cause and update procedures accordingly to prevent recurrences.
By addressing these common issues proactively and maintaining a culture of vigilance, laboratories can ensure a safer working environment and reduced likelihood of safety lapses.
Conclusion
Managing chemical hazards in the lab is a multifaceted process that requires diligence, planning, and collaboration. By implementing these ten methods, laboratories can significantly reduce the risks associated with hazardous chemicals and create a safer environment for research and experimentation. Thanks for reading our blog post on how to manage chemical hazards in the lab! We hope you found it helpful and informative.